CASE STUDIES

CASE STUDY 1
INDUSTRIAL FACTORY
Fire and Gas Detection Systems
Overview:
To develop a cost-effective solution for the Fire and Gas Detection Systems of an extensive industrial factory by redesigning, procuring and programming the central monitoring system for new, existing and future sections (plants, workshops and buildings).
Challenge / Opportunity:
Existing sections had different Fire & Gas Systems from various manufacturers. Any manufacturer of Fire and Gas Panels had specific software and monitoring systems that led our competitors to suggest replacing all existing systems with their own branded solutions.This approach would have been very costly and wouldn’t allow our customer to source and integrate different brands that could meet the requirements for their systems in the future. We believed that we could propose an alternative and intelligent solution that could save money for technical and commercial reasons.


Solution:
After analyzing the systems, our engineers gained a detailed, technical insight into the challenge. As experts in instrumentation, we offered Fire and Gas systems with a general Data Acquisition & Monitoring System based on PLC (Programmable Logic Controller). The system was communicating with Fire and Gas Panels through Modbus RTU. The system- as master- could receive and send data to 32 slave systems on one serial link with the option to easily add additional links at any time.
Outcome:
The customer kept the existing detection systems for existing sections, and we supplied new systems from an unknown manufacturer exclusively for new plants. Also, Data Acquisition & Monitoring System met all their requirements. Our support resulted in a cost-effective solution and assured the customer of maintaining the flexibility of integrating any system that could meet their needs in the future.

CASE STUDY 2
OIL & GAS
Abnormal Pressure Measuring
Overview:
The project consisted of designing and procuring measuring instruments such as indicators, switchers and transmitters for pressure, flow rate, temperature and corrosion. The status reported an abnormal condition of the process; the static pressure was very high (350 bar-g), and operation pressure was about 20 bar-g. And also, the fluid was very viscous and including chloride ions..
Challenge / Opportunity:
Since the fluid included chloride ions, the wetted parts (in contact with the process fluid) couldn’t be 316 Stainless steel. The fluid was very viscous, so the instruments with standard size 1/2” couldn’t be used. We detected a significant variance between the maximum working (design) pressure and operation pressure (ratio 1:17.5 versus the standard 1:1.2); therefore the regular pressure gauges and switches couldn’t be used, and the instrument’s accuracy requirement couldn’t be met. A few competitors suggested using the diaphragm seals as 2” #2500 RTJ with Monel or Hastelloy material for all seal parts (wetted parts including the diaphragm, ring and body).
This solution was costly, and any other manufacturer could not deliver either design a tailored solution to satisfy the customer requirements for Pressure switches and Pressure Transmitters.
.jpg)
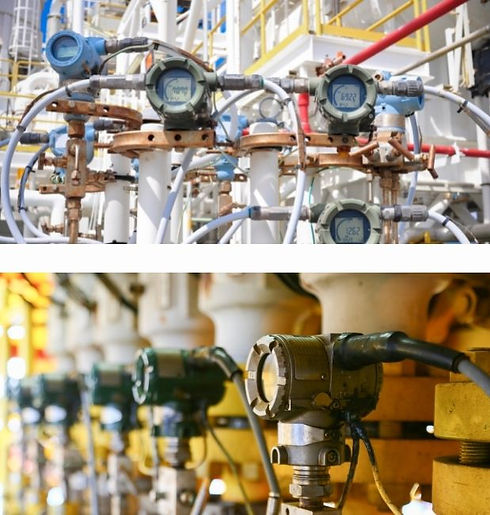.jpg)
Solution:
We proposed a combination scheme of pressure gauges/ pressure switches/ pressure transmitters and a special diaphragm seal as 2” Flanged #2500 RF as well as Duplex stainless steel wetted parts (including diaphragm and face of flange) and 318 stainless steel body. We also proposed the Pressure Limit Valve to prevent any damage to the low-pressure range instruments (max. working pressure of instruments was 25 bar-g).
Our engineers sourced Diaphragm Seals for all instruments from a preferred manufacturer to combine, calibrate, and test all pressure instruments.
As a result, we found three solutions: 1) 2” Diaphragm Seal was used for the viscous fluid, 2) Duplex stainless steels wetted parts were adopted to robust against chloride ion, and 3) the high static pressure was limited by using Pressure Limit Valve.
Outcome:
The proposed Diaphragm Seal was cost-effective compared to other offers and by using the proposed scheme, we could supply all items from valid manufacturers so that all technical requirements and safety concerns could be met. The result was a value-engineered solution that could save money, time of supply and ensure accuracy and safety for all instruments, which led to technical and commercial advantages.

CASE STUDY 3
WATER & POWER
Water Desalination and Electrical Power Plants
Overview:
The customer was a Water Desalination and Electrical Power Plants that used natural gas. Instead of being stable and continuous, the gas supply was shut down at any pressure drop, which resulted in a high cost due to pauses in production, electricity and water, and restart costs.
​
Challenge / Opportunity:
The client had several sudden shut down that they didn’t recognize the reasons. We checked the process and investigated the different possible causes. Finally, we found that the gas supply was dropping suddenly and rising in a short time. The pressure drop in the gas supply resulted in a shutdown since it could not be controlled because the problem was in the upstream side of gas transmission and compression systems. The upstream facility was out of control for the customer.
​
.jpg)
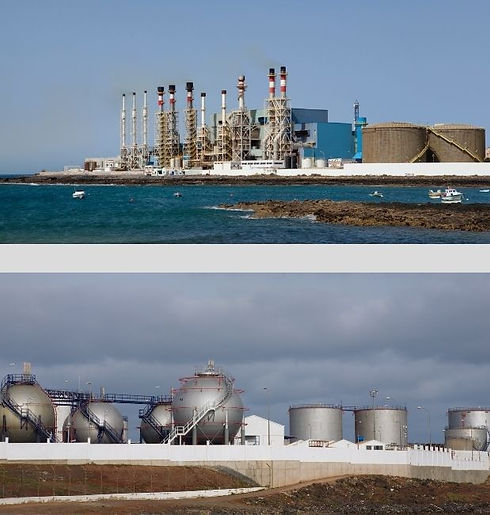.jpg)
Solution:
We offered a very rapid, secure and exact monitoring system for the pressure of gas supply in different system locations, such as the beginning and end of the pipeline and at various places of process. This system monitored the gas supply pressure and prepared a secure and accurate prediction of pressure drop. Also, we designed another automated system to balance out any sudden pressure drop. In this time, the monitoring system predicted a pressure drop with enough time for the compensation system, and the automated compensation system compensated for the pressure drop. Our solution successfully prevented an unpredictable shut down of the system due to pressure drop of gas supply.
Outcome:
The plants stopped suffering from sudden and unpredictable shutdowns to continue without further delays. Also, the proposed system avoids many shout-downs and saves the cost of the restart of plants. So, the customer will have a more secure and safe production of water and power, and the cost of operation is reduced.